液壓數控快速沖床性能、特點概述:
數控液壓沖床是機械沖床的換代產品,它集合了沖床和單柱液壓機的優勢。既可以沖孔,切角,裁斷,壓制,也可以做拉伸,成型。真正實現了一機多用。
數控液壓沖床采用了plc集中控制,全觸摸屏操作。可手動和自動自由控制,機器運行更平穩,噪音小,精度高。危險系數為0。
如果配上自動送料無需人工操作,真正實現了一人多機的操作。
設備所有技術均采用程序操作,行程,速度,拉伸,無需人工調節。
適用對象如下:
汽車 冶金 航空 船舶 日用五金 家電建材 LED燈具 篩網 沖孔標志
附屬功能:壓力顯示、計數顯示、行程顯示、速度顯示、時間顯示、 故障顯示
動作順序:普通沖床使用
快速下行---加壓沖裁--快速回程---恢復遠點
普通壓機使用
快速下行----快轉慢----開始壓制---保壓-----快速回程----恢復原點
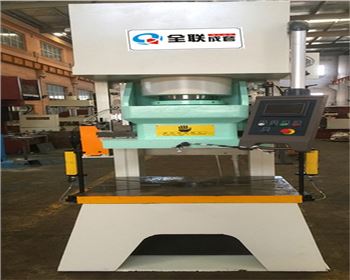
液壓數控快速沖床主要結構及功能介紹:
本液壓機由主機、液壓系統、電氣控制系統和輔助部分組成。
1主機
主機部分由機身、主缸、冷卻系統,及限程裝置等組成。
2機身
機身結構件采用Q235優質鋼板焊接結構,焊后采用退火處理消除內應力,并進行拋丸處理。滑塊及工作臺墊板均有T形槽,可以使用T形槽用螺栓,以便安裝模具(T形槽及中心距尺寸需經客戶確認)。
——滑塊、 滑塊由優質鑄件鑄造而成,然后保持200°進行去應力處理,滑塊置于機身中間,其上平面與主缸連接;滑塊下平面加工有T形槽,用以固定模具;滑塊采用矩形導軌,從而保證滑塊導向精度,剛性好,精度保持性好,滑塊具有很好的剛性,能滿足定程壓制的要求。
3主油缸
本機主油缸為機械擋塊缸,油缸安裝在機架上,通過油缸鎖母鎖緊,活塞桿表面進行耐磨處理,油缸均選用進口的密封件密封,使用壽命長,密封性能可靠,重復定位精度高。
4液壓系統
液壓系統是產生和分配工作油液的裝置,并使主機實現各種動作。油箱為鋼板焊接件,采用封閉結構。箱內裝有過濾器,箱壁開有窗孔以便清洗油箱;設有液位計,油箱上面裝有集成體、油泵電機組等。本機液壓系統使用的主要液壓元件:
5油泵電機組
系統采用一臺4級的電動機經聯軸器各驅動一臺MCY14-1B軸向柱塞泵為液壓系統提供壓力油。
主油泵采用國產恒功率軸向柱塞泵,該泵較大的特點是隨著系統壓力升高,流量成正比減小,保持功率不變,有效節約能源。
5液壓集成控制閥
液壓集成控制閥采用國產二通插裝閥集中控制,具有調壓、換向、保壓、卸荷、支撐、快慢速轉換、超壓保護等作用。主缸下腔控制塊上設有二級防滑塊下落裝置及安全閥,當滑塊在任意位置停止時,該裝置自動關閉,確保滑塊的可靠性和安全性;當其下腔由于閥塊卡死而封閉時,旁路安全閥及時起排油作用,避免安全事故發生。
6充液閥
充液閥安裝在主油缸頂部,當滑塊依靠自重快速下行時,泵的來油不能及時供應主油缸上腔,此時主油缸上腔形成負壓吸開充液閥主閥,使充液筒內油液大量流入主腔,從而達到滑塊快速下行的速度要求,當滑塊回程時,控制油液先頂開預泄小閥芯,使主缸上腔卸壓后,然后打開充液閥主閥,使主缸上腔油液排回沖液箱內,再經過回油管流入油箱。
7電氣系統
整個電氣系統分為動力部分和控制部分。
8動力部分
采用三相四線制交流380V電源,由自動空氣開關、斷路器、熱繼電器、交流接觸器和驅動油泵用的三相鼠籠型感應電動機組成,電機采用Y-△啟動,安全可靠。
9控制部分
控制部分:采用全觸摸屏移動組合控制組成,主控制臺放置在主機左側。電氣柜采用冷軋鋼板制作,靜電噴塑,其內部裝有PLC可編程控制器及其他控制元件等。面板上各種控制按鈕及功能轉換開關、各電機啟停按鈕、各部分監視指示燈及計數器等。移動操作臺主要用于數控自動操作,其上設緊急停止按鈕等。
——控制裝置:采用PLC可編程序控制器控制;
——操作方式:點動、全自動兩種操作方式;
——工作方式:普通壓機和沖床交換。